Why Top Quality Packaging Equipment Service Matters for Your Business
Why Top Quality Packaging Equipment Service Matters for Your Business
Blog Article
Expert Packaging Devices Solution for Seamless Procedures
In today's hectic production environments, the importance of expert packaging devices solution can not be understated. Such solutions not only improve operational effectiveness yet also play a crucial role in lessening downtime and making certain product high quality. By leveraging competent service technicians for preventative upkeep and timely repair work, companies can browse the complexities of machinery monitoring (packaging equipment service). However, the landscape of tools service is progressing, offering both obstacles and chances that require more exploration. What aspects should companies take into consideration when spending in these vital solutions to protect their one-upmanship?
Relevance of Professional Solution
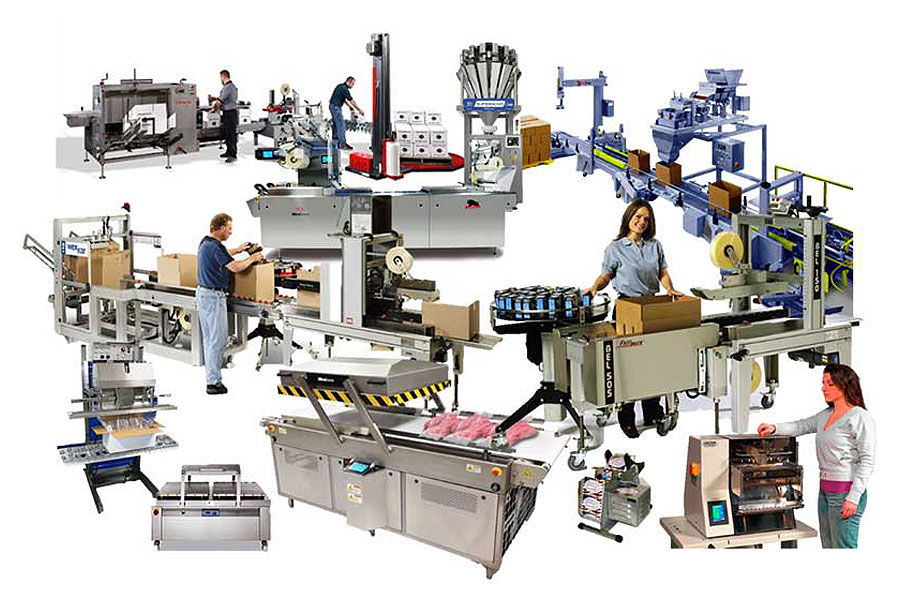
Furthermore, regular servicing by specialists assists lengthen the lifespan of product packaging devices. Expert solution companies are outfitted with thorough expertise of different machinery types and market standards, enabling them to carry out preventative upkeep effectively. This proactive method not just lowers the possibility of unpredicted malfunctions yet additionally enhances general operational dependability.
Additionally, experienced solution can significantly add to compliance with regulative criteria. Product packaging tools must follow strict security and high quality standards, and expert specialists make sure that these criteria are fulfilled consistently. This not just safeguards item integrity yet also secures the company's online reputation.
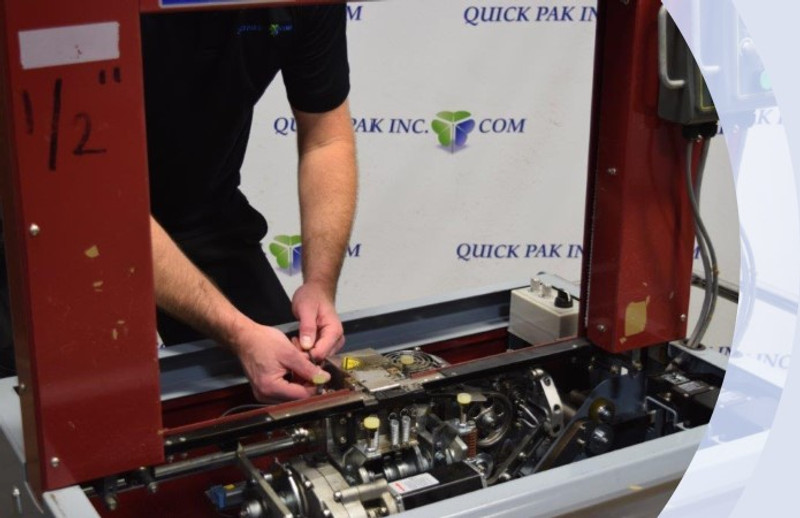
Advantages of Specialist Support
Involving specialist assistance for product packaging equipment not just improves operational performance however also supplies a variety of fringe benefits that can significantly impact a business's profits. Among the most noteworthy advantages is the reduction of downtime. Specialist service technicians can swiftly identify and resolve problems, making certain that assembly line remain active and minimizing the economic losses connected with still machinery.
Furthermore, specialist assistance commonly consists of preventative upkeep, which can prolong the life-span of product packaging tools. By consistently servicing machinery, prospective issues can be determined and dealt with prior to they rise right into pricey repair work or replacements. This proactive strategy not just saves money but also improves product high quality by guaranteeing that equipment operates within optimum criteria.
In addition, leveraging the proficiency of experienced specialists can bring about improved conformity with industry guidelines. These experts remain updated on the most up to date requirements and can guide organizations in carrying out finest methods, therefore staying clear of potential legal responsibilities.
Kinds Of Product Packaging Tools Solutions
When it pertains to product packaging tools solutions, companies can pick from a selection of alternatives customized to fulfill their details requirements. These solutions typically fall under numerous groups, each designed to improve functional performance and minimize downtime.
Preventative maintenance solutions focus on regular assessments and maintenance jobs to make sure that tools runs smoothly and reduces the chance of unanticipated breakdowns. This positive technique can extend the lifespan of machinery and improve productivity.
Repair solutions are essential for dealing with devices breakdowns or failures - packaging equipment service. Competent service technicians diagnose the issues and perform required repair work, making certain that the machinery is restored to optimal working conditions quickly
Setup services are critical when presenting brand-new product packaging tools. Specialists handle the setup, making sure that the machinery is incorporated properly right into existing lines and features as meant.
Educating solutions offer personnel with the needed skills and expertise to run tools have a peek at this site effectively. This training can cover every little thing from standard procedure to innovative troubleshooting.
Last find out this here but not least, seeking advice from solutions use calculated understandings into maximizing packaging processes, helping companies determine areas for enhancement and execute finest practices. In general, choosing the right combination of these solutions can significantly enhance product packaging operations.
Key Features to Search For
What crucial attributes should businesses think about when picking packaging tools services? Most importantly, experience and experience are important. Suppliers with a tested track document in the industry can offer vital insights and options customized to particular functional needs. Additionally, the accessibility of detailed assistance services, including installment, maintenance, and troubleshooting, ensures that companies can count on timely support when problems develop.
One more secret attribute is the flexibility of solution offerings. A provider that can adapt to evolving organization requirements, such as modifications in production quantity or packaging requirements, will contribute in maintaining effectiveness. Technology combination must be a top priority; modern-day packaging equipment solutions must include sophisticated innovations, such as automation and real-time monitoring, to boost performance.
Last but not least, online reputation and client comments should not be ignored. Engaging with testimonials and case researches can give a more clear photo of a company's dependability and quality. By taking into consideration these crucial attributes, services can make enlightened decisions that will sustain their packaging operations and add to general success.
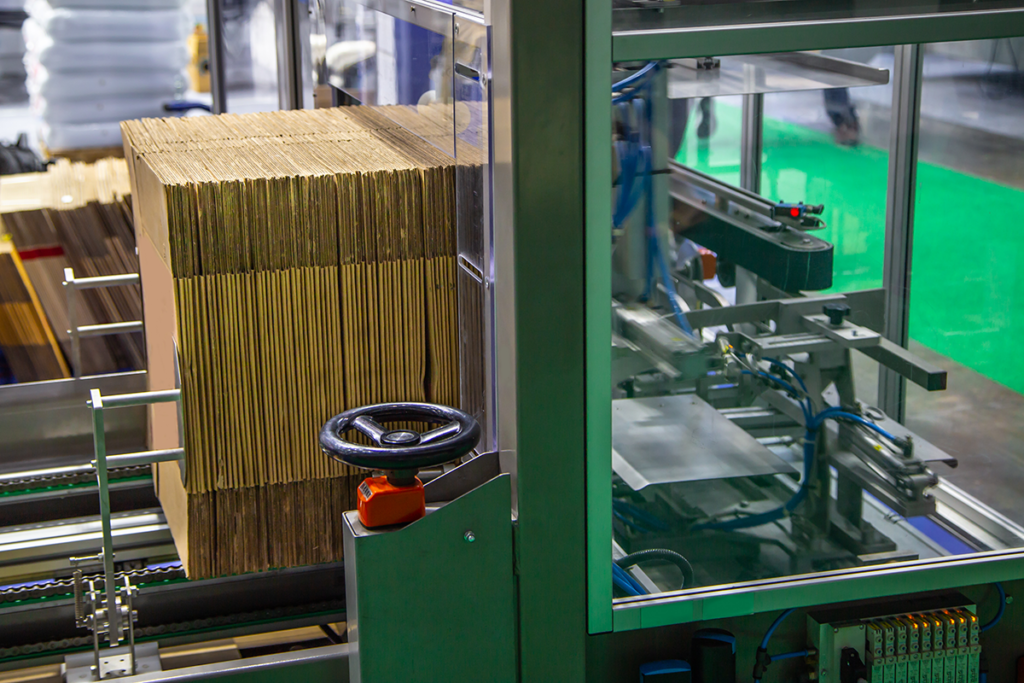
Investing in Long-Term Success
Purchasing lasting success in product packaging devices services calls for a critical technique that prioritizes sustainability and scalability. Firms should concentrate on selecting devices that not only satisfies existing functional requirements but additionally fits future growth and technological improvements. This foresight decreases interruptions and improves general efficiency.
A crucial element of this financial investment is the routine upkeep and service of tools. Establishing a proactive service schedule reduces downtime and expands the life-span of equipment, eventually causing cost financial savings. Partnering with professional provider guarantees that the equipment is optimized for performance, therefore preserving high manufacturing standards.
Furthermore, integrating innovative modern technologies, such as automation and IoT connection, can considerably boost functional abilities. These innovations allow for real-time tracking and data analysis, allowing companies to make educated choices that align with their lasting goals.
Last but not least, spending in employee training on new modern technology and finest techniques fosters a culture of continual renovation. By growing a knowledgeable labor force, organizations can adapt to changing market needs and maintain their one-upmanship. Inevitably, an all natural method that includes equipment, solution, innovation, and labor force growth placements firms for continual success in the see this site product packaging industry.
Verdict
Finally, expert packaging equipment solution plays a pivotal role in guaranteeing seamless procedures within manufacturing environments. The combination of preventive maintenance, rapid repairs, and thorough training considerably boosts devices reliability and reduces downtime. By prioritizing these solutions, companies can attain optimal operational efficiency and prolong the lifespan of their equipment. Eventually, purchasing expert assistance fosters long-term success, enabling organizations to maintain high item quality and competitiveness in an advancing market landscape.
Report this page